Axenic System is one of the leading company engaged in architectural
designing, planning, installation, commissioning of HVAC and Turnkey
construction for cleanroom projects
Air Showers
Table of Contents
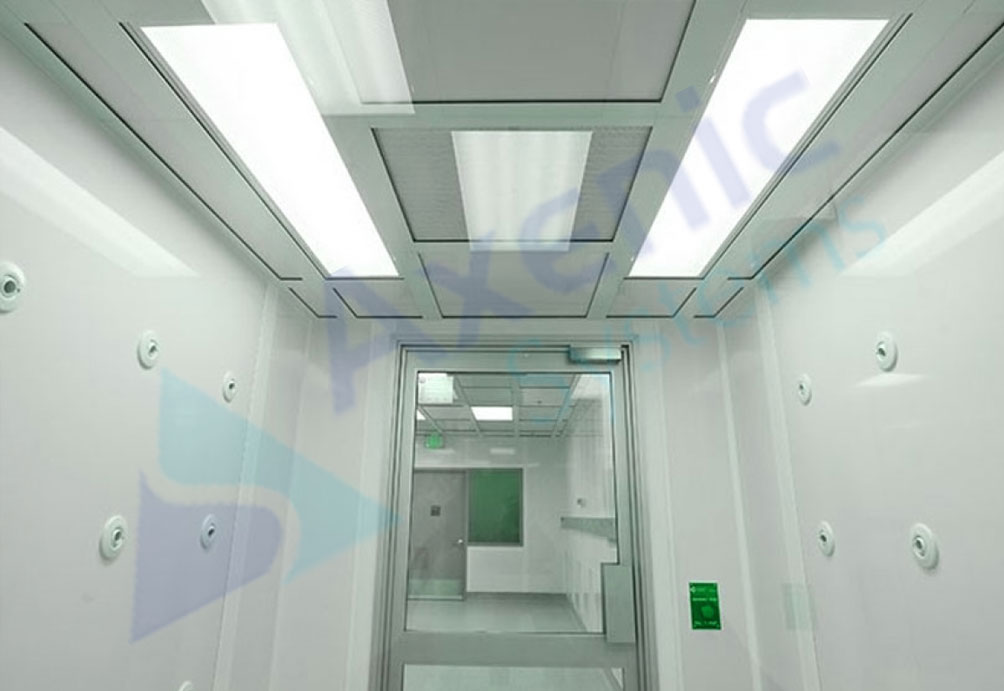
Introduction to Air showers
AXENIC SYSTEMS (established in 1995) is one of the leading companies engaged in manufacturing and supplying Air showers to carry out the decontamination process in a cleanroom. Our finest quality Air Showers are wisely constructed at our factory, tested at different parameters then dispatched to the client’s site. We have an in -house facility of design, production and installation of air showers for laboratories, clean rooms and manufacturing areas.
Air showers are additions particularly designed for the removal of particles from people or materials, prior to their entry or exit from certain clean areas. They are independent air recirculation systems installed at entries to cleanrooms and other controlled environments. Air showers permit the cleaning of the particles that remain deposited in the operator’s clothing or materials and are primarily used in the income to clean areas with high classification necessities, such as sterile areas, and exits of areas in containment.
Air showers are basically a cabin like structure particularly prepared to eliminate dust particles and polluting products that may be deposited in personnel’s work materials or clothing at the entrance or exit of clean or containment areas.
Technical specifications of Air Showers
Model | Tunnel – 1 | Tunnel – 2 | Tunnel – 3 | Tunnel – 4 | Air Shower w/o Bottom Board | |
External Dimension (mm) | 1290 x 800 x 2060 | 1540 x 1000 x 2050 | 1540 x 1200 x 2050 | 1540 x 1600 x 2050 | 2100 x 2100 x 2050 | 2300 x 5200 x 2150 |
Internal Dimension WxHxD (mm) | 800 x 760 x 1910 | 800 x 960 x 1910 | 800 x 1150 x 1910 | 500 x 1550 x 1910 | 800 x 1960 x 1910 | 800 x 4960 x 1910 |
Nozzles | 6 – One Side | 12 – Two Sides | 16 – Two Sides | 18 – Two Sides | 24 – Two Sides | 60 – Two sides |
Blow Power | 550W | 100W | 1500W | 2000W | 2200W | 7500W |
HEPA Filter Dimension | 550 x 610 x 120 – One Piece | 610 x 610 x 120 – Two Pieces | 915 x 610 x 120 – Two Pieces | 1220 x 610 x 120 – Two Pieces | 610 x 610 x 120 – Four Pieces | 610 x 610 x 120 – Ten Pieces |
Suitable Person | 1 Person w/ one side blowing | 1 Person w/ two sides blowing | 1 – 2 Persons w/ two sides blowing | 2 – 3 Persons w/ two sides blowing | Cart | |
Nozzle Diameter | 33 – 38MM | |||||
Air Shower Time | 0 ~ 120 seconds Adjustable | |||||
Spurt Wind Speed | 17~26 m/s | |||||
Power | 440V AC, 50 Hz, Three Phase Connection | |||||
Filter Efficiency | 99.99 % | |||||
Cleanliness Level | Class 1000/ Class 100/ Class 10/ Class 1 | |||||
Noise level | Less than 55 db | |||||
Shower jet velocity | More than 20±2 meter/second | |||||
Door | Steel fabricated with safety glass & electromagnetic locks | |||||
Construction | GI Powder coated / SS 304 / 316 Stainless steel | |||||
Standard fittings |
|
|||||
Optional |
|
|||||
Design Options |
|
Air Shower Design Considerations
Air shower designs and configurations accommodate precise requirements for industry, as well as the number of people using the cleanroom. Modular cleanroom entrance systems also simplify shipping and assembly.
The quantity of people that need to enter a cleanroom in each amount of time will have a major impact on the size of the air shower and filtration system that is needed. Designs range from single batch systems where one person uses the shower at a time, to tunnel systems for bigger groups to pass through quickly. Tunnels are becoming more common because of the quantity of cycle time required for a shift change.
Using a 90-degree design, users enter on one side and exit to the right or left at a 90-degree angle. This allows the air shower, with nozzles on two opposite walls cleanses the workers easily. In this configuration it has less air nozzles than the straight-through design and needs the worker to turn 360 degrees to ensure that they’ve been thoroughly purified.
- Other designs may have dual doors or even three doors for entry and exit. Configurations include cart/parts-cleaning air showers, which are used for conveyors, carts, pallets and constant-part operation.
- Low-profile air showers accommodate facilities with ceilings less than 96 inches.
- ADA compliant air showers are sized so a wheelchair can turn around in the air shower.
How an Air Shower Works
Air showers function likewise to automated car wash pressure washer systems, using several steps throughout the decontamination procedure. The following cleanroom air shower specifications procedure details the operational characteristics of a cleanroom air shower.
- The worker passes through the entrance door and a sensor triggers interlock magnets, which lock the air shower and cleanroom doors.
- Several adjustable nozzles blow high-velocity streams of Class 100 clean air onto the worker.
- The high-velocity air generates a flapping effect on clothing which produces a cleansing action, eliminating particulates from cleanroom garments.
- To make sure all particles are removed, workers raise their arms and revolve in place.
- Indicator lights signal at the end of the cleaning sequence, and the cleanroom door opens.
Moreover, it takes four to eight seconds of cleaning time and another two to four seconds for the air shower to eliminate contaminated air before the worker can exit. Computerized microprocessors control the cleaning and wait times linked with the air shower decontamination procedure.
Construction of Air shower
As for their construction appearances, Air showers are generally made of stainless steel. They contain two doors; one for entrance and another one for exit, with a gasket and electromagnetic interlocking system that prevents its simultaneous opening and while the cleaning cycle is in progress. In case of emergency, Air showers are equipped with an internal and external push-button that terminates the operation and blocks off the doors. The interlocking device of the doors averts the simultaneous opening of both, thus creating an efficient barrier that prevents the exchange of air between areas of different classification and therefore, the transmission of particles.
The equipment has a programmable controller, which manages all the operating parameters of the equipment, including the flow of people, the triggering time of the fan, or the delay in opening the doors. Its process is produced by a presence detector once the doors are locked. An emergency button is installed inside the cabin to interrupt the air cleaning cycle and unlock the doors if needed.
The operation, duration and characteristics of the cycle, and even the chance of differentiating between input and output cycles are completely programmable and adjustable according to the user’s requirements through a simple control system, which lets the equipment operate automatically.
Application industries
- Defence research Lab
- Pharmaceutical Industry
- Chemical Laboratory
- Animal Facilities
- Gold Producers
- Cloth Manufacturer
- Semi-conductor Laboratory
- Electronics Industry
- Food Testing Laboratory
Search For Tags:- air shower manufacturers, air shower clean room price, air shower, air shower for clean room, air shower use, air shower specifications, air shower working principle